Name | Description | Materials | Color | Texture |
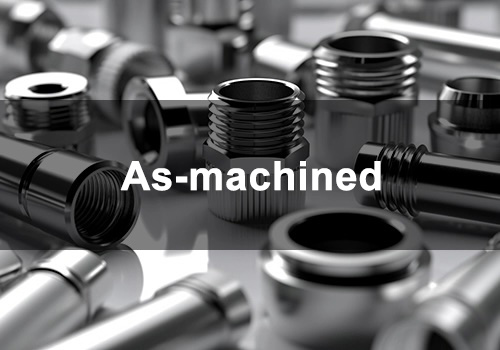 | Our standard finish for parts is called "as machined" finish. This type of finish has a surface roughness of Ra 3.2 μm (126 μim), and all sharp edges are removed and parts are deburred. You may notice visible tool marks on the surface. Please note that this finish meets the requirements specified for non-cosmetic availability. | All materials | N/A | Stain |
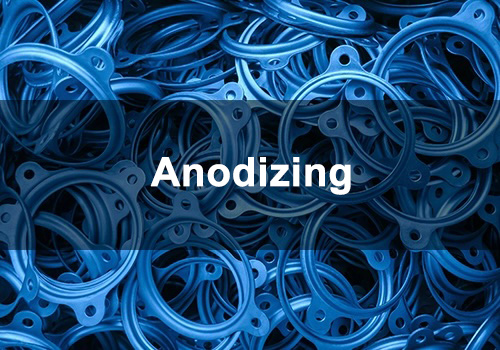 | Anodizing increases corrosion resistance, wear resistance, and hardness while maintaining the surface of the metal. | Aluminum | Gold, blue, clear, black, red, grey | Matte smooth finish |
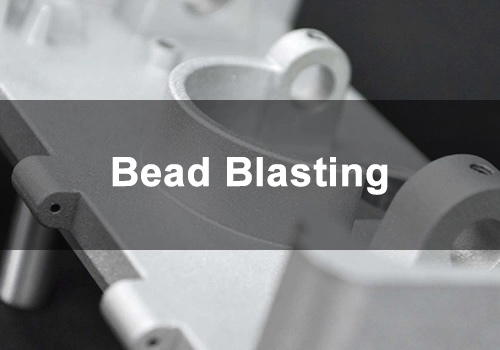 | The surface of the parts or product is left with a matte finish. It is mainly used for aesthetic purposes. | Steel, Stainless Steel, Aluminum, Brass, Copper | N/A | Stain |
 | In this surface-treatment technique, rough belts are utilized to leave marks on a material's surface. This is typically done for aesthetic reasons. | Steel, Stainless Steel, Aluminum, Brass, Copper | N/A | Stain |
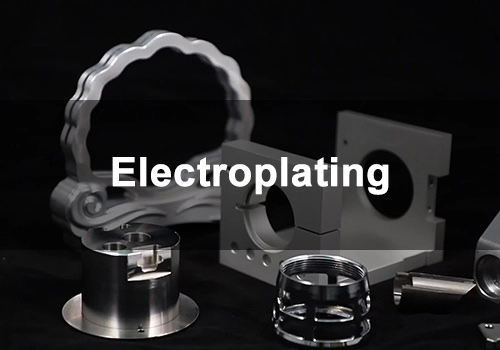 | This includes decorative and functional options. Electroplating is another example, as it is a way to manipulate properties using electrical tools. | Stainless Steel, Steel, Aluminum | Black, Grey, Clear, Gold, Blue, Red | Glossy, smooth finishh |
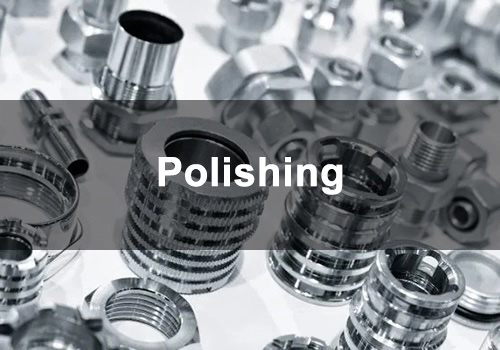 | Polishing is the process of giving an object a shiny, smooth surface by rubbing it or using chemicals. | Steel, Brass, Stainless Steel, Aluminum | N/A | Glossy |
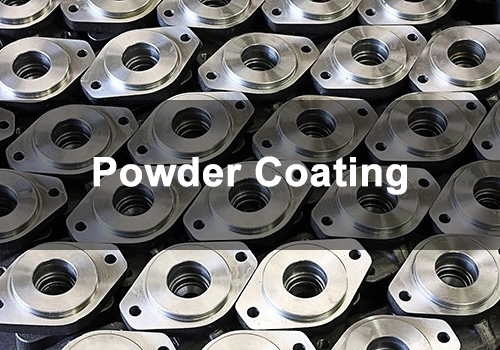 | Powder coatings use a free-flowing, dry powder. Electrostatically applied powder coatings are then hardened with heat or UV. | Steel, Stainless Steel, Aluminum | Black, Pantone number, or RAL code | Semi- glossy or glossy |
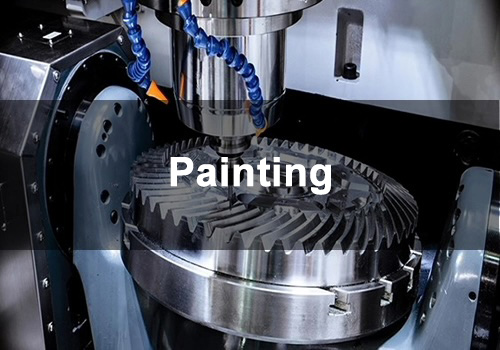 | Die castings can be painted with various coatings for specific color, texture or protective properties. Paint finishes range from basic painting to more advanced techniques such as electrostatic painting or dipping. | Aluminum, Stainless Steel, Steel | Black, any RAL code or Pantone number | Semi- glossy or glossy |
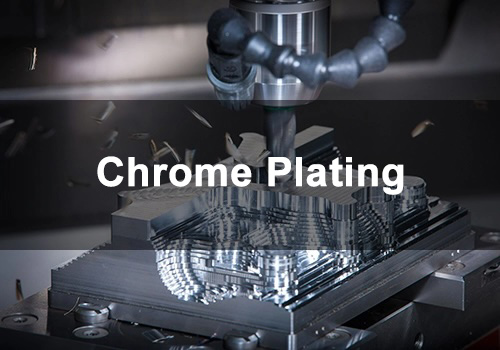 | Chrome plating is the process of depositing a thin layer of chromium on the surface of die castings by electroplating. This process produces a shiny reflective finish and offers excellent corrosion resistance. | Stainless Steel, Steel, Aluminum | Black, Grey, Clear, Gold, Blue, Red | Semi- glossy or glossy |
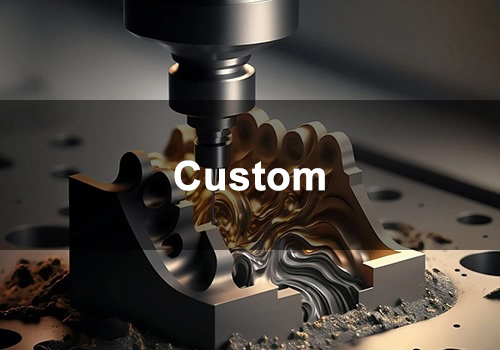 | You can choose from different custom finishes depending on your materials and end-use. | All materials | N/A | N/A |